設計ガイドライン
PA 11
General guidelines
Wall thickness
In general, we recommend a wall thickness of at least 1 mm. Large parts may require larger wall thicknesses or added ribs or fillets for reinforcement. It is possible to have thinner features with walls of only 0.5 mm for living hinges, but here, the length needs to be limited to 10 mm when they are only attached at one end, or 25 mm when attached from two sides.
Although hinges can be positioned differently without the risk of breaking (thanks to the isotropic mechanical characteristics of the material), it is advisable to avoid making the thinnest sections of your living hinges parallel to the Z plane.
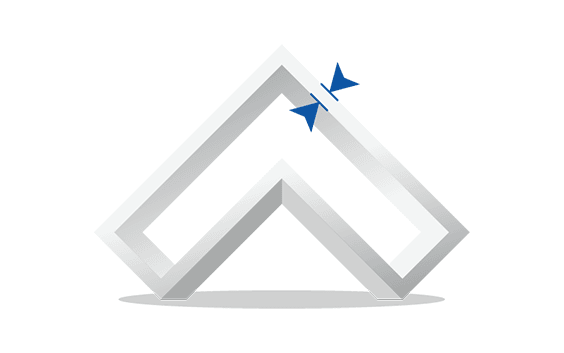
Hollowing
We advise hollowing out a solid model as much as possible, and when the wall thickness exceeds 20 mm. This will save material and prevent sink marks. We recommend a wall thickness of 2-3 mm and the inclusion of at least two holes with a minimum diameter of 2 mm for powder removal.
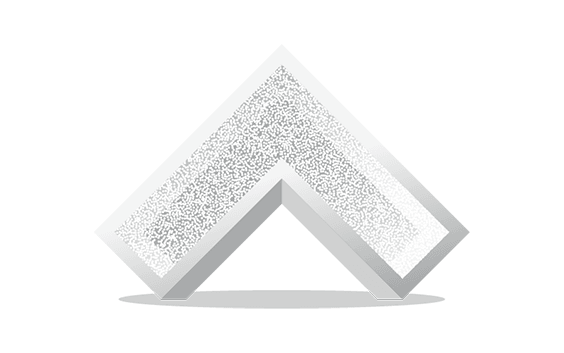
Holes and channels
It is possible to create holes or perforations and internal channels. For holes and perforations, the recommended diameter size is 2 mm, with a minimum of 1 mm, but some post-production will be needed to remove excess powder.
Longer internal channels can be difficult to clear out, especially if the powder is partially fused together. In general, complex holes or ducts require larger diameters to achieve thorough removal of the unfused powder. We recommend a diameter of at least 3 mm for internal channels. Some residual powder may be stuck on the inside of complex channels. It is advised to design a strip or chain through the channel to help in dislodging the powder once the part has been printed.
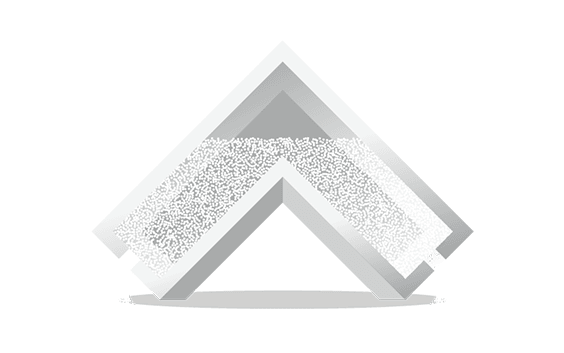
Interlocking parts
It is possible to print interlocking parts and assemblies in a single build. Parts that are printed together should have a minimum clearance of 0.5 mm.
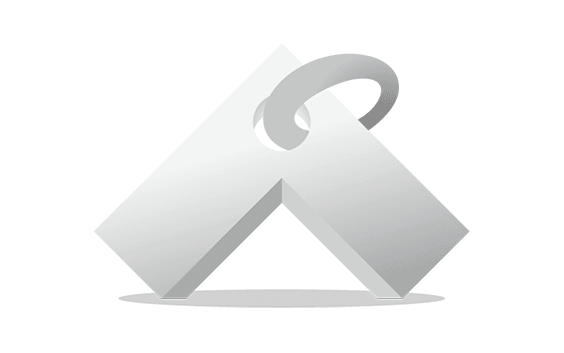
Lattice structures
Lattice structures allow you to reduce weight and material. Keep in mind that you must maintain a minimum gap of 1 mm between the lattice beams so the unfused powder can be removed.
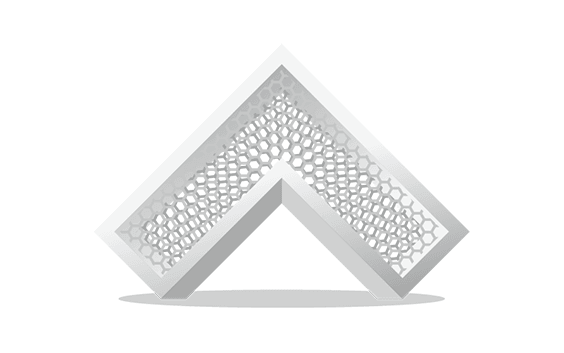
Assembly
When designing parts that need to be assembled, it’s important to maintain enough distance between the parts. A perfect fit in your CAD software does not necessarily ensure a perfect fit after printing because your software ignores the friction present in the real world. Therefore, always leave at least 0.3 mm between the different parts. For parts with large surfaces and wall thicknesses, you will need to maintain even more distance between the parts. In cases like these, please get in touch with our team to check printability.
In order to help us print your parts with the best possible dimensions for assembly, please design your files with an orientation equal to the relative orientation of your parts in the final assembly.

Embossed and engraved details
For embossed or engraved textures, we advise a minimum thickness of 0.25 mm. For legible engraved or embossed text, we recommend letters with a minimum line thickness of 0.5 mm, a depth of 1 mm, and an overall height of at least 2.5 mm.
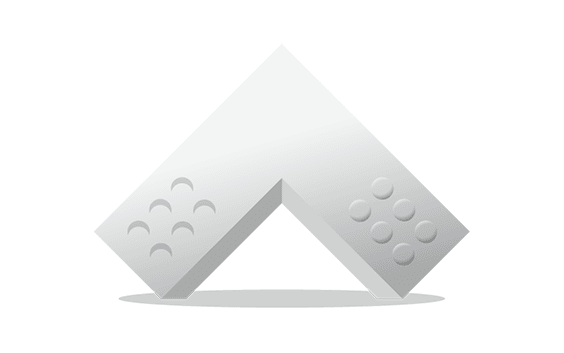
Warpage and deformities
We strongly recommend that you do not design large, flat plains in dimensions like an A4 page. In most cases, your model will deform. This process is called “warping”. Creating support ribs under your plane does not solve the problem, but rather increases the chance of deformation even more. The key here is to avoid large flat planes.
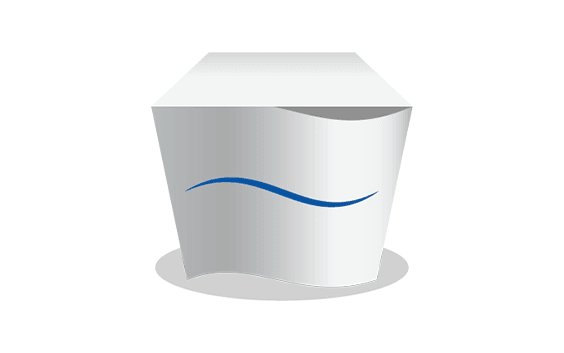
Guidelines for smoothing
To achieve a smooth finish, your part is put into a tumbler with small stones that vibrate at a high frequency to smooth the part’s surface.
Strength and fragility
Several factors make it hard to fully predict the outcome of the polishing process. One of these is the geometry of your part, which can act differently each time it is put in the tumbler. In general, you should have wall thicknesses of at least 1 mm throughout your part.
Although we carefully place and orientate your parts in our printers to minimize “weak points” created by the layered buildup of your part, certain elements of your design may be more sensitive to the impacts of the polishing stones than others. Therefore, we suggest adding some extra wall thickness if your design can allow for it. Smoothing is not advised if your part has tiny details like pins because they are likely to break off during the polishing process.
The largest dimension of your part should not be more than 200 mm, as bigger parts can get stuck during the smoothing process. The smallest dimension should not be less than 30 mm, as smaller parts can break in the process.

Interior polishing
The small size of the polishing stones means that they can easily get stuck inside small holes. Therefore, we recommend that any openings that need polishing should be larger than 6.5 mm in diameter. This helps prevent stones from getting stuck inside your model.
Also, note that the inside of your model will always be less polished than the outside. In fact, your part will not be polished at all on the inside if the holes are smaller than 6.5 mm because the stones will not be able to enter.
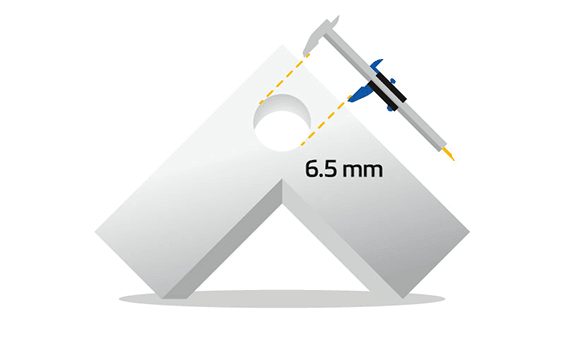
Rounded edges
If your part contains sharp edges, these will be rounded off. Rounded corners and smooth transitions between surfaces will have a higher degree of polishing than sharp edges.
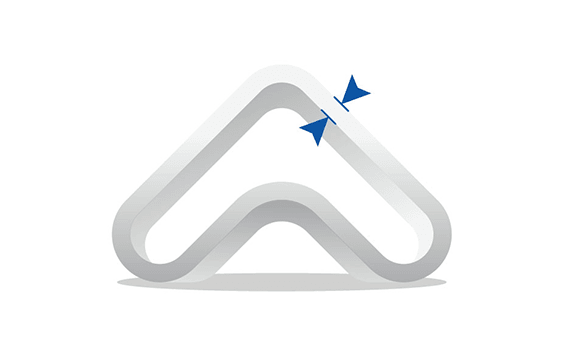
Embossed and engraved details
Embossed details on your model tend to be worn away by the polishing stones. Make sure to raise these details by at least 1 mm, otherwise they may disappear when your model is polished. Engraved details are less of a problem because, in most cases, the stones won’t be able to reach the inside of the engraving; however, the edges may still be affected. To be on the safe side, make sure your engravings are deeper than 1 mm.
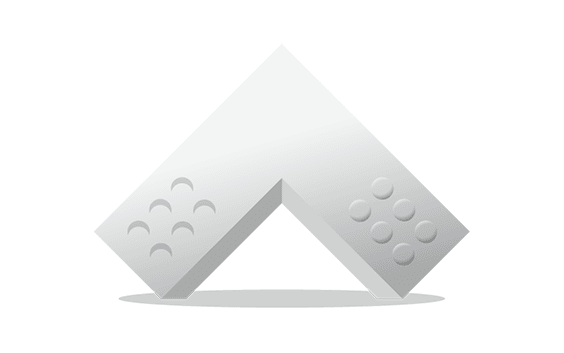
File requirements
We accept file formats STL, 3DS, 3DM, OBJ, WRL, MATPART, STP, SKP, SLDPRT, STEP, CATPART, IGES, MODEL, MXP, and MGX on Materialise OnSite.
As well as the need to respect these file formats, there are also constraints related to the content of those files. To deliver the best possible quality and ensure traceability, we only allow one model per part to be ordered via our online platform OnSite.
This means per file, there can only be one shell. If there are multiple shells in one file, we will only process it as it is recognized as one model or part meaning that the shells are intersecting or interlocking each other (if applicable see the technical specifications below). Otherwise your part will not be processed correctly.

技術仕様
Maximum part dimensions | 370 x 274 x 375 mm |
Standard accuracy | ±0.3% (with a lower limit of ±0.3 mm) |
Layer thickness | 0.09 mm |
Minimum wall thickness | 1 mm |
Minimum detail size | 0.25 mm |
Interlocking or moving parts | Yes |
Internal channels | Yes |
Surface structure | Grainy structure with stone-gray color |