PODCAST
3D Printing Eyewear and Design
Thinking differently — how to make the most of 3D printing when designing eyewear
- Subscribe:
- Apple Podcasts
- |
- YouTube
- |
- Spotify


In our 3DP&Me series, we talk to some of the world’s foremost designers to find out and explore the special relationship these individuals have with all things additive.
This episode dives into the concept of ‘design freedom’, and looks at what this phrase really means for 3D printing eyewear. In particular, a discussion on how designers can fully leverage the opportunity to think about and work differently with form, materials, color, and even functionality.
- Subscribe:
- Apple Podcasts
- |
- YouTube
- |
- Spotify
Read the full transcript
Alireza: Welcome to the second episode of 3DP&Me podcast by Materialise. I am Alireza Parandian, one of the founders of the business line eyewear, and I am responsible for global business strategy and commercial activities here. In today's episode, we'll be diving into one of my favorite topics, design freedom, looking at what this phrase really means for eyewear designers that are interested in using 3D printing. In particular, we'll be discussing how designers can fully leverage the opportunity to think about, to be different, work different, with materials, colors and functionality even.
Helping me in this episode is one of my good friends and an ally in setting 3D printing for eyewear industry, Fabián Hofmann. The man needs little introduction. In my opinion, he is an eyewear designer, brand consultant, interior designer, architect, creative genius. Fabián, would you like to introduce yourself?
Fabián: Well, you already did it. I mean, you just talked about everything that I'm doing professionally. Yeah. I'm pleased to be part of this podcast series. So, thank you very much for inviting.
Alireza: So Fabián, let's get to it immediately. I think it's fair to say that you're regarded as one of the champions, at least by me, in the 3D printing of eyewear realm. But I don't think many know that your love affair with the technology started already way back. Could you reflect for our audience?
Fabián: Yeah. That was like many years ago. I think it was beginning of the NOTIS, like of 2000, something like that. It might even have been 1999 when my first company that I founded. We were doing a lot of homeware stuff and furniture. So, we had a project going on with porcelain, and it was so complicated that we needed to find a way in making the prototypes fast. So, we want it to have perfect circular molecular bowls, and it was impossible. So it was the first contact that I actually started working with stereolithography. We were basically able to, to have a lot of prototypes done in parallel and very fast. So the process was possible at all.
So for me, that was the first contact, but back in that time, it wasn't something that was made for going into production or making a real product out of it. It was really something like rapid prototyping. So, I love it. Ever since then, I never lost contact with this technology. But over the last years, it has become one of the main means of doing stuff in the design world. So, it's a change.
Alireza: Yeah. Since we got to meet each other, I think it was seven, eight years ago during SILMO, right?
Fabián: Something like that. It's been ages. That was the start of a very, very interesting journey. As we both know, we have been working together in many projects now.
Alireza: Fabián we met, I think it was 2014. How do you see this world of 3D printing of eyewear evolved since then with materials, with the technology, with everything that has become possible and even by the brands?
Fabián: I mean, when I remember eyeglasses was just starting at Materialise, so probably the machines weren't as calibrated and perfected as they are now. What I can say, it has been a rapid change. I'm glad that I have been invited to be part of that because I remember that in the beginning I was in Leuven quite often. Then we had discussions and we had workshops.. I enjoy that because it gives me a chance as a designer to be part of an emerging technology. That means that I'm not only a client, we can actually talk to you guys, and that is a very unusual thing.
Alireza: Fabián, I know that during the past years we've talked a lot about what 3D printing enables. We've talked specifically about this topic of design freedom and what that means and what that entails for a designer. One of the things that you've been always reflecting about is that freedom of design for a designer can be freedom of thinking. It can set your thinking free. Could you elaborate for our audience that might be interested in that?
Fabián: If you're working in eyewear for a while, you realize that a lot of tooling is needed and that’s the classic production means of making glasses. That means that you have limitations. So you kind of do everything. It's just because most of the methods are completely subtractive. Meaning that you have a block of material where you just mill the not needed material away. You have problems with accessing certain areas with a tool. So when you start working with 3D in the 3D world, you are free. You can walk around in your design because you can just zoom in. You can go into detail.
I think one possibility is freedom of design to see it from a standpoint of making a pretty design. So you can add little patterns or stuff like that, but personally I'm not interested in that. What I think is interesting is that you can go into a more engineer based thinking, so you can actually design stuff that couldn't be done otherwise. That is the one thing that makes it so interesting because that for me as a designer and also for my colleague, Coerte, that's the complete freedom of design. So for us, we always come from a standpoint of being engineers. We really want to know how things work. Then when you have found out how the whole material reacts, and if you have the properties nailed down, then the freedom begins.
Alireza: One of the challenges that I hear from designers and engineers often face when they want to start with 3D printing is that they actually want to hold on to what they know already from the traditional materials or technologies that they have available at their disposal. That's tempting obviously to try to think like that. That is a little bit in contradiction with what you mentioned as what is the freedom of thinking. What do you think about that, and what would your advice be to the designers that want to get started with 3D printing?
Fabián: Well, it's understandable because you are used to how you do a pair of glasses let's say in acetate or even in metal. When you're a good designer, you have done that for years. So basically you know your comfort zone. So you can design whatever you want because you know in the back of your head already it works like this and I have to think about that. Well, if it comes to the manufacturer, I have to talk to them about that. This is basically understandable, but it doesn't work that way. So when you see the first designs of companies that actually start doing 3D, it's very close to the 2D world. But the feeling, although it was made into 3D processes, is still like it could be something that you easily could do in a 2D process.
So what you really have to wrap your mind around is that you have to be very clear. I don't have the limitations of just diving into the material with a tool, and then just mill something out. You can do different things. I mean the thing is that you really are completely free. And that is difficult because if you don't know in which direction you want to go because probably everything is possible, your mind can go rampant. I cannot give advice on how to actually tackle the thing. But forget about 2D. That is the one thing. In 3D, you actually really have to move in the 3D world. You just have to be familiar with moving in space and you have to have a feeling for the scale because well everybody knows that on a computer, you just consume indefinitely.
So the one thing that I would say is get as much information about the material, what it can do, the tolerances and the material properties and everything. Then start doing something that you would never have dreamt of doing in 2D. But that is, I cannot enforce it enough, it's a completely different world.
Alireza: I think Fabián every journey is a little bit different. You know what I've been putting an emphasis on all the time that we know each other, that every brand must look at their own DNA and try to make the most out of it to be able to reflect their DNA. Can you explain a little bit about your journey in working with even different materials within the 3D printing realm trying to combine different things. It's a search that you did as well, and give people some insight into that search. It went sometimes the wrong way and you found your journey again.
Fabián: Well, we've both been there. We tried right in the beginning, and I think it must have started five years ago, we tried to combine printed polyimide with printed titanium. So that was my journey because that is the question of freedom of design, and I thought you could do everything. What we did, and I'm quite open about that, we printed screws. That is really something that I think nobody has tried because we were talking about the tolerances and everything. Well, we did succeed in some way, I must say, but in the end we realized that some things may be back then, and I'd say like five years ago, weren't where they are now.
This was I was deviating from the path a little bit and I was trying out other materials. But again, now with the knowledge that I have that you can also work with metals that can be printed. Now that I know how to treat these metals afterwards and what has to be taken into account, I might even think about doing something again in that direction. But what I would give as an advice to other people who start doing that is that you have to be prepared that it doesn't work immediately because it's not that the technology is not safe or it doesn't work at all. It's just the thing you get used to the material you get use to the process of designing the whole stuff., although it's not like a prototyping anymore, but the good thing is you can have prototypes pretty fast and you should do that. You should try out and go like several steps and really get a feeling for it, even go for different surfaces or coloring, whatever.
So this is all accelerating the whole process, and that's really interesting to do so, and take your time. If you're working for a company and they go like, "So yeah, I've heard 3D printing is going to be like totally radical and we want that too. So, can have results in three weeks time?" Probably you could have results in three weeks time, if all the 3D data are okay, but the problem is you don't know what it is. Then you said you had a point before where you said it's also very important to keep the DNA of a brand in your mind. So when you go start with a new technology and a new material and everything is completely new, you also have to find out if it's still part of your company. So take your time.
Alireza: And isn't that beautiful? I mean, part of that trying out in the beginning is part of that learning journey that you want to embark on. You want to learn how you can mix and match different things, that you have available for you to be able to reflect that DNA of your brand, right?
Fabián: That is the truth, and you should take our time. But I couldn't be more enthusiastic about it because it has given us so many chances that we didn't have before. What I can say that's also very interesting, it's not all about production but it's also about the whole process. So maybe you don't need these super high MOQs that normally would be needed in 2D produced stuff because you have to make sure that the tooling is somehow financed and all this is not needed in 3D.
So, first of all, you can have fast results. You can try out whatever you want until you have something in your hands that you really like. Then you can be sure that will be the end product. So also if you want to make that a capsule collection in the beginning, so let's say a company has never worked with 3D stuff and the designer has a good idea. So start with something that is very small and sexy, but perfect, and that could be a start. Then the company can have the feel of if it really is exactly what they're looking for.
Alireza: I fully agree with that. I mean, you need to start small, get to learn new things, but can't you agree with me? I think you, but also others have collaborated with us during the past years, and you have definitely challenged us as well in that journey. So it has been as much of a learning experience for us at Materialise as it has been for you guys. I think we're super grateful for all of that collaboration because the innovation that is a result of that has been tremendous and wonderful. That the result is the products that people can witness.
Fabián: Yeah, but the thing is if you give designers or clients the chance to be part of this whole thing, and I know that you started that so many years ago, that was the co-creation process. That's also like I tackle architecture. So, I never go to a client and tell him what he needs because that's arrogant. I mean, the client wants to have a nice place. The client has needs in how they want to set up the whole building. So you have to listen closely and you have to find out what your client wants. Then you start going... That's very, very similar to what we're doing here with the eyewear and with Materialise. Then you just go on a journey together. You'll find out what is needed and then basically you can enable these people, your client to actually get what they want.
This co-creation process is really interesting. I mean, it's just like I had this discussion with a friend of another brand, and he's also a designer and a very good designer. He was saying basically it's a deal with the devil because we're just giving you really valid information. But on the other hand side, that's very good because we get exactly what we want. So if we're not telling you what we want, giving away information, then we are not getting what we want. So this is a trusting, and this is like a partnership thing. So, I'm not calling like Materialise and say, "I need that." It's basically just every time we do something new, we find out how we can do it, and then we talk to the different departments. That means coloring, that means like surface treatment.
Alireza: I think that would be interesting for our listeners to understand, you've obviously come a long journey, but you have Neon Berlin as your own brand together with your colleague. Can you describe to our audience when an idea sparks in your head, what do you go about?
Fabián: Yeah. I mean, as a designer and I also can speak for my colleague, Coerte, there because we are design team and we do most of the stuff together, the thing is that we always think about a story. That's very interesting. So for me, it's boring to say, let's make some nice panto styles. So that would not be the way how I start a project. So I have always a story in mind. It could be something from science fiction or it could be something with the check a story like a submarine story. Then in that process, we just find out how the whole collection is supposed to look. So what do we want to achieve, what we want to do. Then this kicks in. Okay. Then we have the freedom to design whatever we want and we can go rampant. It's basically whatever we imagine comes to life. So, this is a very interesting thing. You just start with a story. You have a collection in front of you. Then you just jump, and that is one of the rabbit holes that you go down.
Alireza: That is truly being a digital artisan, creating that story, because what you want to create is beauty. That is an emotional response that you can enable with the people that will use that product. That requires something that is called digital artisanship, which you can pick and mix the right materials, like you do in NEON Berlin. Can you elaborate on that a little bit?
Fabián: This is exactly what we're doing. We see each other as engineers, as designers, even as architects, but at the same time there is art to it. The emotional aspect is very important. So you are basically creating a product that is for the customer, and they want to have a feeling when they wear it because they need to connect. At the same time, you also have to have the functionality in mind. So, what we did is, some people might know from the past I founded a titanium company in 2012 with two investors. So, I was actually working with metal glasses for quite a long time for several years and we really tried to reinvent this product.
So when I started the new company with my colleagues, then it was absolutely off the table that we could do something in metal. You can understand that because then people would have gone, "Okay, he's just going back to the past. He's copying himself. They just have no ideas." But I like the idea. What I have learned with a metal glasses, with a rim glasses that you have to think different. If you have a pair of acetate glasses, you just have a slap of plastic and you cut out the eye holes, you cut out the outer shape, and then you have a pair of glasses. I mean, there is a lot of more steps needed to make that glasses, but that's basically just roughened up.
So what makes that so interesting is you have always an outside and an inside the shape and you can play with that. So that is very typical for horn, wood or acetate classes. If you have metal glasses, if they're not cut out of any metal slab, then basically you just have a wire. What happens is that the design must be more focused and more centered on the lens. That's very interesting because you don't have anything that you can add to the glasses, or you don't have any material left where you can design. You just have the shape of the glasses and then you have a wire, which is just accompanying the glass is just wrapped around it.
So, this is what we did when we started doing the first collection for Neon Berlin, the BCRA collection. We thought about designing something like wire frames, So what happened is we had to come up with algorithm, with tools that are completely different. So in our world, we are not just actually projecting something and then subtracting it. It's basically the first step that we do is we just walk around in 3D space. That's very interesting. Our designs, they don't even look like designs. We just have the lens shapes, almost like an optician, and then basically our algorithm, our tool knows exactly what we want to do. This workflow is extremely interesting and it's extremely powerful. I think it's also very, very important for the design product in the end. So, you can see it is basically metal look like glasses, but they're not.
Alireza: So you just gave wonderful insights about that design process, right. Taking it one step further, I think when you started to realize how our technology works and where the limitations of 3D printing is and what the possibilities and limitations of the coloring and post-processing are, you really started to co-create that collection in a way that it would make sense in the end product, right?
Fabián: Yeah, it would because coming from an idea that was a 2D technology and also I did have my own ideas how it was supposed to look. Then that is something that goes back to the beginning of our conversation. I realized the product looks different and there are some limitations. When I say limitations, it's not like, as in trance, you can't do it. You just have to do it differently, or you have to accept some stuff that is connected to the material. Now that I come to think of, that's also a very important thing that designers need to know. These processes and the material they have properties and you should work with the properties and not against it. So basically don't try to do something that the material doesn't want you to do. You wouldn't do that with acetate. You wouldn't do that with wood and some of the properties they just come with the material.
Fabián: So, one thing that we should be quite open about is that the material has a surface structure. I know there are processes that can make that look very smooth, and the coloring has become so mature in the last years is that that's really amazing what happened there on this front. But I think as a designer, you should stay true to your product. At Neon Berlin we do that. We keep it as raw as possible. We show how it is done, and that is part of our product. So now I'm closing the circle. What started as metal glasses, like wire frame glasses, has become something completely different. The only thing that is similar is the extreme thinness of the material.
That again is freedom of design because when you know how the material can be reinforced and what you do to make that as thin as possible without it being too flexible or bending it, that's really interesting. So we start from one point and we want to have metal glasses and printed. We don't get that and we don't want it anymore. Then we have something else which is much more beautiful. I think that is, again, the thing of the journey. You have to be prepared to embark on that journey.
Alireza: Fabián, I'd like to thank you very much for joining us in this session. I want to also thank you for the journey that you have followed together with us, I want to ask you a last question. How do you see the future of 3D printing for eyewear designers?
Fabián: I would say it's a bright future because the materials are getting better. Now that especially Materialise has an own department which is only geared to making eyewear, You start talking to the designers, you listen to what they want, what they need, and that basically is transformed into a completely new kind of workshop that you're offering to the people. So, I would say the more people are starting working with you and the more people are embarking on that journey and experiencing the freedom in design, the more we can accelerate the whole thing.
Fabián: What I think is very important, and that's probably a last thing for me and a lot of people are understanding that too, is the environmental impact on the whole thing. So not having to produce a lot of excess material or not basically throwing away 70, 80, 90% of the material like you do in 2D processes. That's very interesting. Then there come new materials that might come from a completely different source. So maybe in the future, we are working with materials which are not mineral oil based anymore, but they could be plant-based. I mean, I know that it already starts. I think that is going to be a very interesting direction. Coloring is a topic that will change as well. So I can just say what I have seen in the last five or six years that was so fascinating and it was like so fundamental that I'm absolutely sure that in five years time, when we have another talk, we will be astounded both of us, what is possible now. I like that.
Alireza: Okay. Fabián, I'm looking forward to that conversation in five years then. Thank you very much.
Fabián: Thank you very much for having me. It was a pleasure. I wish you a nice day.
Alireza: Thanks to our listeners. If today's topic has got you thinking, we've produced an accompanying guide exploring the design benefits of 3D printing available on www.materialise.com/eyewear. Till next time.
Featuring
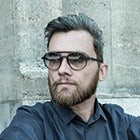
Fabian Hofmann
Founder fhmhofmann
About your host
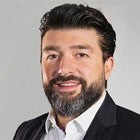
Alireza Parandian
Head of Global Strategy Wearables at Materialise
Share on: